【品質評価レポート】理美容はさみ刃先端状態の定量的把握
- 2021.04.28
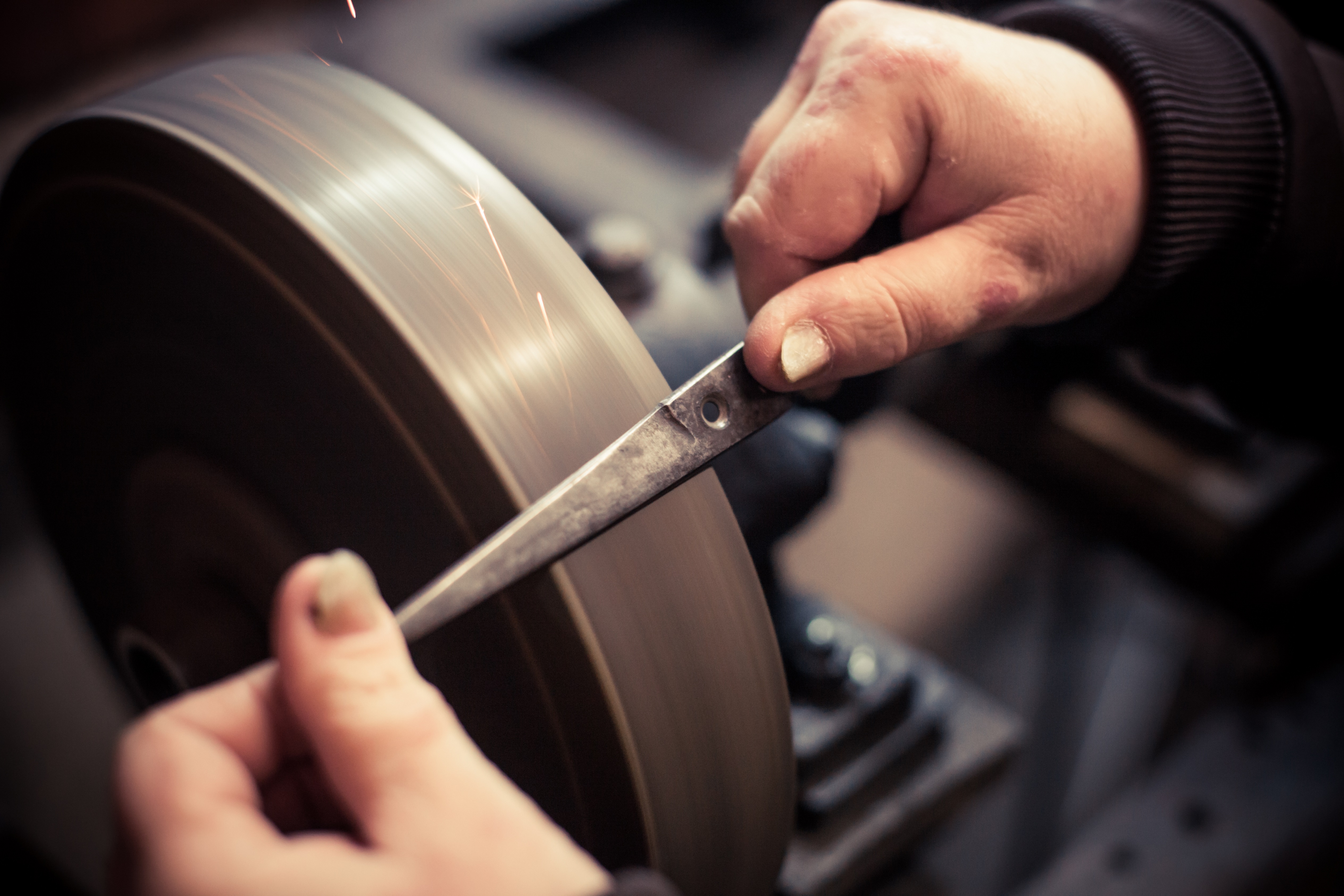
HSCはジャパンクオリティのハサミの技術や性能を守るために発足した団体です。
海外製の粗悪品をmade in japanと謳ったり、勘違いするような表記で消費者を
騙して安価でネット上で販売をしている業者がいるのも事実です。
消費者が、そのことに気づくためにも、正しい情報を広げていく必要があります。
HSCでは消費者の皆様が安心してハサミを購入し、使っていただけるように、ハサミの品質の標準化に取り組んでゆきます。
その一環として、今回は「理美容はさみ刃先端状態の定量的把握」参考文献を紹介いたします。
理美容はさみの刃先端状態の定量的把握 ―刃のざらつき、刃こぼれの評価について―
1.緒言
鋏が使用により切れなくなる原因は、刃先端の状態が変化したことに起因する。そして、その劣化の形態には、二通りあることが報告されている1)。
A.刃先端に変形や欠損(俗にいう刃こぼれの状態)が出来た場合。
B.刃先端が摩耗して、刃先端の半径が大きく(俗にいう刃が丸くなった状態)なった場合。
本報告では、上記A.の状態を定量的に把握する方法と、過去に行った一部の実験について説明する。
2.刃先端の粗さ測定
一般的に金属平面の粗さを測定する方法には、接触針と呼ばれる、先端にφ4μmのルビーを取付けた接触式の針で表面を撫で、その上下動で粗さを測定する接触式のものと、金属表面から反射してくるレーザや光、電子ビームなどの反射の状態から粗さを測定する非接触式のものがある。
非接触式のものは一般的に測定範囲が限定されており、鋏の刃線全体を測定するような用途には向かない。またこれらの方法では、平面の計測が可能だが、測定機に付属する解析ソフトでは複雑にカーブしている刃線の部分のみを取り出して解析を行うことなどは通常できない。
これに対して接触式のものは、一次元的にしか動作しないが、測定距離を長く取れるので、8インチ程度の鋏であっても充分に測定が可能である。加えて、接触式の測定器には通常の接触針とは異なる形状も準備されており、今回は「チゼルエッジ」(Chisel:ノミ、タガネのこと)と呼ばれる楔形の接触針(図1に示すノミの先端のような形状)から発想を得て、自作の接触針を作製し使用した。
測定の様子を図2に示す。チゼルエッジの利点は測定方向をX方向とした時にY方向の影響を除去した上で、面粗さ(Z方向の高さ)を測定できる点にある。
刃線、つまり刃先端の連なりがどのような形状であろうとも、エッジ側先端のくさび部分の幅の範囲内に収まっていれば粗さの測定が可能である。
実際に、鋏のY軸方向の変形量より想定される必要なエッジ幅は最大で100ミクロン程度なので、この方法は現実的な方法であった。
この方法を用いる際に、懸念される誤差要因として以下の三点を考え、事前に検討を行った。
①鋏やエッジの姿勢が狂うと、測定値に影響が出てしまう。
②エッジを接触させることで、鋏の刃先端を削り取る可能性がある。
③同様に、鋏の刃先端によってエッジ側が削られると測定値に影響がでてしまう。
①鋏の取り付け精度
測定時の誤差要因となると思われる鋏の取り付けのズレを図3にまとめる。
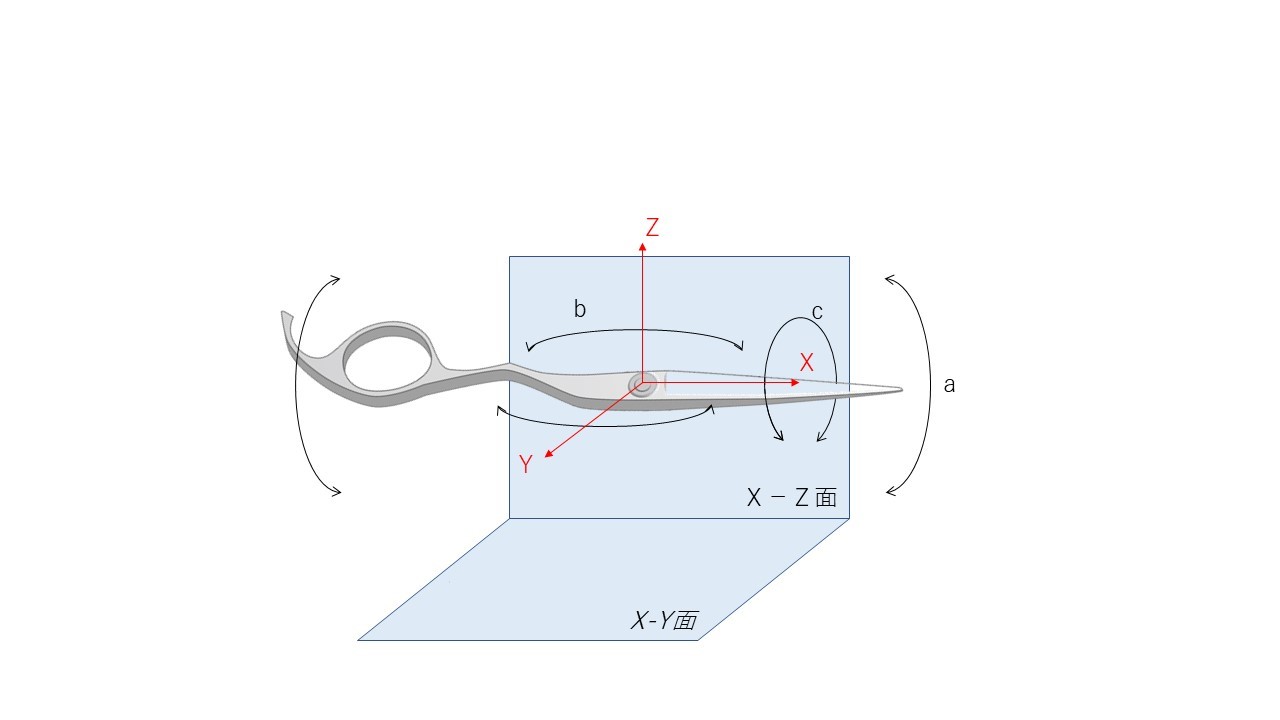
物体は三次元の三つの軸に対して回転することが出来る。はじめに、図3におけるX-Z面に対して平行なaの回転であるが、粗さ計には物体全体の表面のうねりの影響を除外するために低い周波数のデータを除去するハイパスフィルタの機能(カットオフ)がありaの回転が与えられても測定値に影響は生じない。
次に図3の下のX-Y面に対して平行なbの回転について考える。自作したチゼルエッジはチゼルの幅が5mmなので例えば5インチの鋏の刃先端の粗さを測る時、刃渡りがおおよそ50mm、これが5mm傾くと、本来50mmのはずの測定長はピタゴラスの定理から49.7mmと0.3mm短くなるだけなので測定値にほとんど影響は与えない。
最後にcの回転であるが、図2からも分かるように鋏をバイスで固定して触点部分が垂直になるようにしてあるので、この方向の回転はそもそも生じない。
②③測定による刃先端の及びチゼルエッジの欠損
鋭利な状態にある刃先端に対して垂直にエッジを移動させることにより、刃先端もしくはエッジが傷ついて測定値やその後の実験に影響が出ることが想定されたため、繰り返し測定をした場合の測定結果の変化を確認した。
ただし、ダメージが生じた場合には鋏側でなくチゼルエッジ側である方が好ましいと考え、素材の硬度はチゼルエッジ側に柔らかいものを選定した。
図4に一回目と十回目の測定の結果を示す(カットオフ0.8mm、測定長さ3.2mm)。また、図5に測定毎の粗さの推移を示す(Raは粗さの中でも全体的なばらつきを表す指標)。
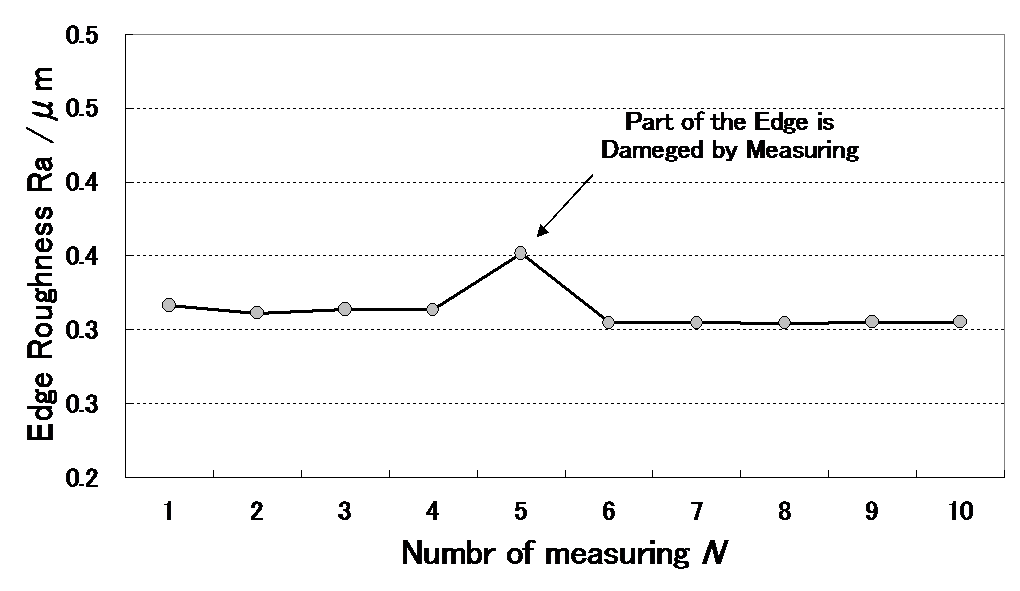
測定プロフィールを比較するとどちらもほぼ同様の形状が得られている。ただし一回目の測定で得られていた図中の○部は五回目の測定時に脱落してしまった。これが原因でRaの推移を示す図5においても五回目の測定だけは値が大きくなっている(六回目以降の測定では測定範囲を狭めて脱落部前までの測定とした)。このように、本測定方法が鋏側の刃先端に与える影響は皆無とはいえないが、その影響は小さい。しかしながら、繰り返しの測定は好ましくないと判断した。
以上のようにこの測定方法は刃先端の状態を定量的に把握するつぁめに有効な方法であることが予想された。しかしながら、刃先端の状態に影響を与えてしまう可能性も皆無ではないため、回数を限定して活用してゆくこととした。
3.実際の測定結果の一例
二丁の鋏を実際の理容室で六週間使用してもらい、粗さの変化を測定した結果が図6である(Rzは一番大きな傷の大きさを表す指標)。
図からわかるように、鋏の使用に伴い刃こぼれが生じ、刃先端の粗さが大きくなっていることが分かる。特にサンプルBの刃先近くでは二週間目の測定後に大きな刃こぼれが生じて値が極端に大きくなってしまっている。
このように、今回説明した方法を使うことで、鋏の刃先端の刃こぼれの状態をかなり正確に把握することが可能である。
3.結言
鋏の刃の状態を把握するために粗さ測定器を利用して刃先端の粗さを測定する方法を考案した。
1)三次元的にカーブする刃先端を刃渡りに沿って測定するためには、接触式の粗さ測定機にチゼルエッジを組合わせて測定する方法が有効である。
2)考案した測定方法は測定結果の再現性も高く信頼できるが、刃先端にダメージを与える場合もあり、繰り返して何度も測定を行うことは好ましくない。
3)実際のサロンワークで使用している鋏について、二週間おきに測定を行ったところ、使用に伴い粗さが大きくなり、刃が傷んでいる様子を把握することが出来た。
刃先端の劣化については、今回示した刃こぼれが生じたために切れが悪くなる場合と、刃先端が摩耗して切れが悪くなる場合がある。後者に関しては別に説明を行う予定である。
参考文献
1) 井上ほか:平14塑連合講論 (2002),53.
2) 井上ほか:塑性と加工,45-522 (2004), 540.
3) 井上ほか:塑性と加工,47-543 (2006), 66.
鋏が使用により切れなくなる原因は、刃先端の状態が変化したことに起因する。そして、その劣化の形態には、二通りあることが報告されている1)。
A.刃先端に変形や欠損(俗にいう刃こぼれの状態)が出来た場合。
B.刃先端が摩耗して、刃先端の半径が大きく(俗にいう刃が丸くなった状態)なった場合。
本報告では、上記A.の状態を定量的に把握する方法と、過去に行った一部の実験について説明する。
2.刃先端の粗さ測定
一般的に金属平面の粗さを測定する方法には、接触針と呼ばれる、先端にφ4μmのルビーを取付けた接触式の針で表面を撫で、その上下動で粗さを測定する接触式のものと、金属表面から反射してくるレーザや光、電子ビームなどの反射の状態から粗さを測定する非接触式のものがある。
非接触式のものは一般的に測定範囲が限定されており、鋏の刃線全体を測定するような用途には向かない。またこれらの方法では、平面の計測が可能だが、測定機に付属する解析ソフトでは複雑にカーブしている刃線の部分のみを取り出して解析を行うことなどは通常できない。
これに対して接触式のものは、一次元的にしか動作しないが、測定距離を長く取れるので、8インチ程度の鋏であっても充分に測定が可能である。加えて、接触式の測定器には通常の接触針とは異なる形状も準備されており、今回は「チゼルエッジ」(Chisel:ノミ、タガネのこと)と呼ばれる楔形の接触針(図1に示すノミの先端のような形状)から発想を得て、自作の接触針を作製し使用した。
図1 ノミ
図2 測定の様子
測定の様子を図2に示す。チゼルエッジの利点は測定方向をX方向とした時にY方向の影響を除去した上で、面粗さ(Z方向の高さ)を測定できる点にある。
刃線、つまり刃先端の連なりがどのような形状であろうとも、エッジ側先端のくさび部分の幅の範囲内に収まっていれば粗さの測定が可能である。
実際に、鋏のY軸方向の変形量より想定される必要なエッジ幅は最大で100ミクロン程度なので、この方法は現実的な方法であった。
この方法を用いる際に、懸念される誤差要因として以下の三点を考え、事前に検討を行った。
①鋏やエッジの姿勢が狂うと、測定値に影響が出てしまう。
②エッジを接触させることで、鋏の刃先端を削り取る可能性がある。
③同様に、鋏の刃先端によってエッジ側が削られると測定値に影響がでてしまう。
①鋏の取り付け精度
測定時の誤差要因となると思われる鋏の取り付けのズレを図3にまとめる。
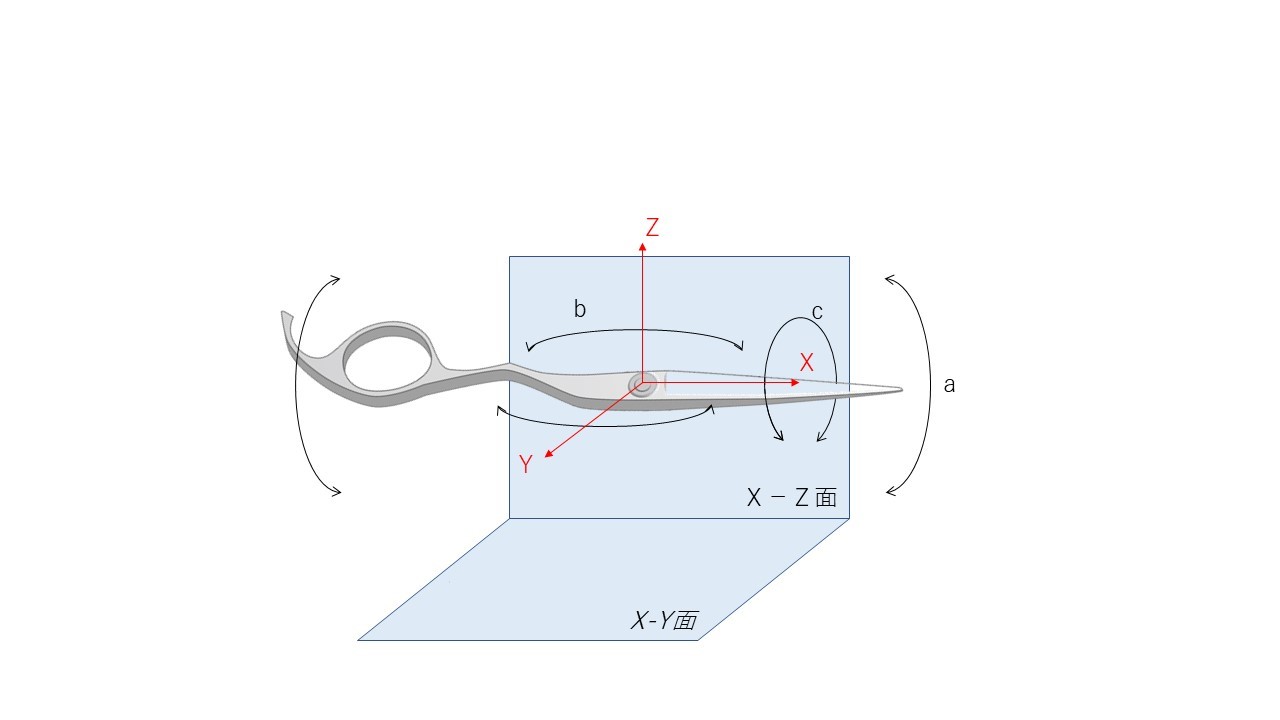
図3 取り付け姿勢の影響
物体は三次元の三つの軸に対して回転することが出来る。はじめに、図3におけるX-Z面に対して平行なaの回転であるが、粗さ計には物体全体の表面のうねりの影響を除外するために低い周波数のデータを除去するハイパスフィルタの機能(カットオフ)がありaの回転が与えられても測定値に影響は生じない。
次に図3の下のX-Y面に対して平行なbの回転について考える。自作したチゼルエッジはチゼルの幅が5mmなので例えば5インチの鋏の刃先端の粗さを測る時、刃渡りがおおよそ50mm、これが5mm傾くと、本来50mmのはずの測定長はピタゴラスの定理から49.7mmと0.3mm短くなるだけなので測定値にほとんど影響は与えない。
最後にcの回転であるが、図2からも分かるように鋏をバイスで固定して触点部分が垂直になるようにしてあるので、この方向の回転はそもそも生じない。
②③測定による刃先端の及びチゼルエッジの欠損
鋭利な状態にある刃先端に対して垂直にエッジを移動させることにより、刃先端もしくはエッジが傷ついて測定値やその後の実験に影響が出ることが想定されたため、繰り返し測定をした場合の測定結果の変化を確認した。
ただし、ダメージが生じた場合には鋏側でなくチゼルエッジ側である方が好ましいと考え、素材の硬度はチゼルエッジ側に柔らかいものを選定した。
図4に一回目と十回目の測定の結果を示す(カットオフ0.8mm、測定長さ3.2mm)。また、図5に測定毎の粗さの推移を示す(Raは粗さの中でも全体的なばらつきを表す指標)。
図4 一回目と十回目のプルフィール
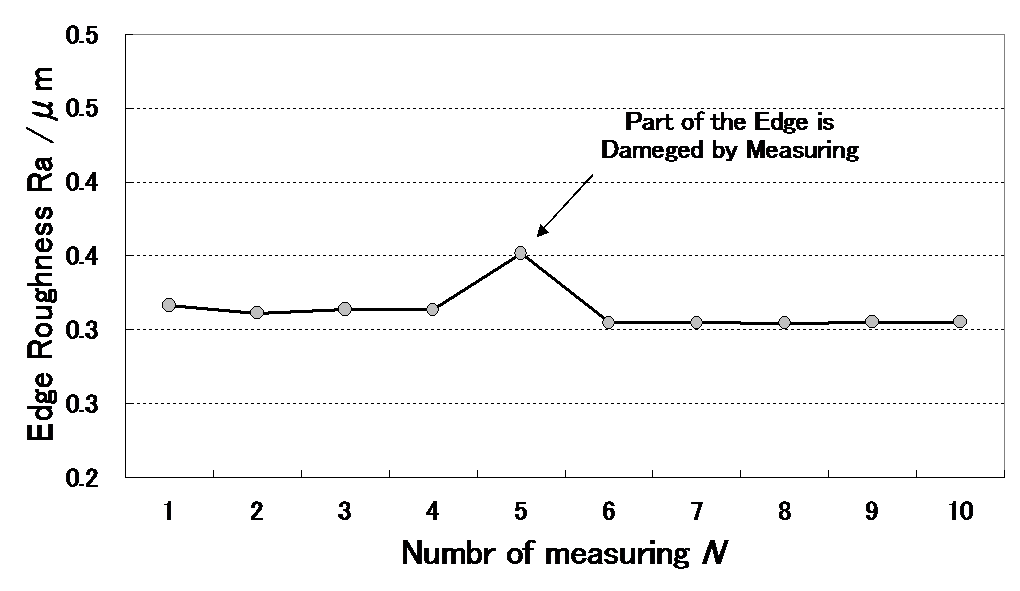
図5 測定値の変化
測定プロフィールを比較するとどちらもほぼ同様の形状が得られている。ただし一回目の測定で得られていた図中の○部は五回目の測定時に脱落してしまった。これが原因でRaの推移を示す図5においても五回目の測定だけは値が大きくなっている(六回目以降の測定では測定範囲を狭めて脱落部前までの測定とした)。このように、本測定方法が鋏側の刃先端に与える影響は皆無とはいえないが、その影響は小さい。しかしながら、繰り返しの測定は好ましくないと判断した。
以上のようにこの測定方法は刃先端の状態を定量的に把握するつぁめに有効な方法であることが予想された。しかしながら、刃先端の状態に影響を与えてしまう可能性も皆無ではないため、回数を限定して活用してゆくこととした。
3.実際の測定結果の一例
二丁の鋏を実際の理容室で六週間使用してもらい、粗さの変化を測定した結果が図6である(Rzは一番大きな傷の大きさを表す指標)。
図からわかるように、鋏の使用に伴い刃こぼれが生じ、刃先端の粗さが大きくなっていることが分かる。特にサンプルBの刃先近くでは二週間目の測定後に大きな刃こぼれが生じて値が極端に大きくなってしまっている。
このように、今回説明した方法を使うことで、鋏の刃先端の刃こぼれの状態をかなり正確に把握することが可能である。
図6 実際の実験結果の一例
3.結言
鋏の刃の状態を把握するために粗さ測定器を利用して刃先端の粗さを測定する方法を考案した。
1)三次元的にカーブする刃先端を刃渡りに沿って測定するためには、接触式の粗さ測定機にチゼルエッジを組合わせて測定する方法が有効である。
2)考案した測定方法は測定結果の再現性も高く信頼できるが、刃先端にダメージを与える場合もあり、繰り返して何度も測定を行うことは好ましくない。
3)実際のサロンワークで使用している鋏について、二週間おきに測定を行ったところ、使用に伴い粗さが大きくなり、刃が傷んでいる様子を把握することが出来た。
刃先端の劣化については、今回示した刃こぼれが生じたために切れが悪くなる場合と、刃先端が摩耗して切れが悪くなる場合がある。後者に関しては別に説明を行う予定である。
参考文献
1) 井上ほか:平14塑連合講論 (2002),53.
2) 井上ほか:塑性と加工,45-522 (2004), 540.
3) 井上ほか:塑性と加工,47-543 (2006), 66.