Quality Evaluation of Hairdressing Scissors (Lecture)
- 2021.02.01
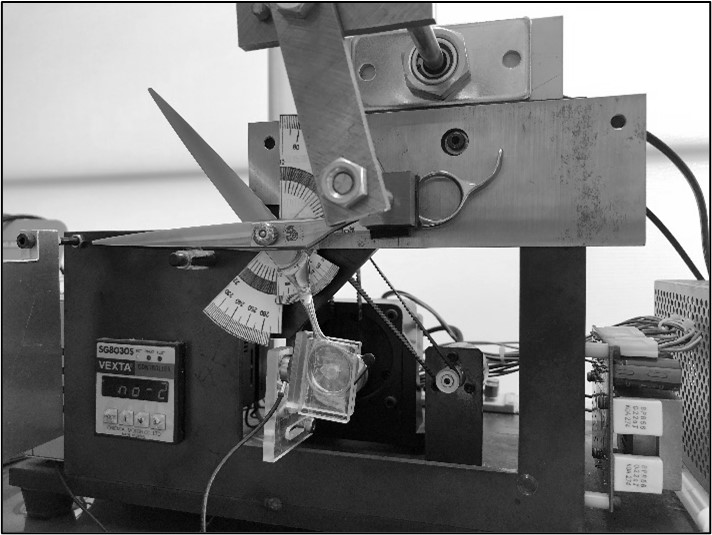
Quality Evaluation of Hairdressing Scissors (Lecture)
HSC is working on standardizing quality of hairdressing scissors, and some of the research results were lectured in “the 71st Joint Lecture on Technology of Plasticity”* which was held on the WEB from November 14, 2020. The outline of the lecture contents is explained below.
HSC will continue to work on standardizing quality of scissors based on science, so that users can purchase and use scissors without worry.
*Secretary Society: The Japan Society of Technology of Plasticity, Cosponsored by: The Japan Institute of Light Metals, The Japan Society for Precision Engineering , The Japan Institute of Metals and Materials, The Japan Society of Mechanical Engineers, The Society of Materials Science Japan, The Iron and Steel Institute of Japan, The Copper Society of Japan.
Kenji Inoue (Tokosha Co., Ltd.) PhD, Member of JSTP
Koshi Yamamura (Yamamura-mfg co., Inc.) PhD, Member of JSME
Toshio Hasegawa (Naruto Scissors Co., Ltd.)
Makoto Hagino (Utsumi Co., Ltd.)
Shinichi Takahashi (Hikari Co., Ltd.)
Takashi Iimura (Iwate Industrial Research Institute) PhD, Member of JSPE
At present, there is no globally unified standard for quality of hairdressing scissors. The main reason for this is that elucidation of the cutting mechanism has not progressed. Specifically,
For changing this situation, we set up Hairdressing Scissors Consortium (HSC) last year. We aim to create environment that hairstylists can choose scissors based on scientific evidence.
We listed evaluation items for quality of scissors (Table1). Left side corresponds to right side of table. Items users evaluate with their feeling is on the left side of table. Parameters that may make the difference is on the right side of table.2) In this report, we report about compatibility of blades.
2.Testing machine
Fig. 1 is picture of testing machine. This machine consists of air cylinder for clamping scissors, motor for rotating, load cell for measuring force to push up, and rotary encoder for measuring rotation angle. Closing load measured by load cell is transferred to data logger through strain amplifier. Recorded data can be analyzed by PC.
2.1 Evaluation of magnitude of variance
Because hairdressing scissors are finished by hand, variance of quality is large. Therefore, we measured variance at first. We prepared five samples of same model. At first, we choose one sample and put on the testing machine. We measured necessary force for rotating a blade when screw of scissors is totally tightened, and confirmed approximately 0.34N is necessary.
We adjusted the screw to make maximum closing load without cutting 0.49N±5% of +0.15N.
We measured closing load five times repeatedly (Test1). Next, we measured five times again by using same samples but scissors are put off from testing machine each time to understand variance effected from clamp (Test2). And finally, we adjusted to make maximum closing load without cutting 0.49N, and measures five samples, one time for each (Test3). The data when output voltage of the encoder changes (every 0.52 deg) was extracted, and the average of 5 times was obtained. The variance for each measurement was calculated and compared. The results are shown in Fig. 2.
In Fig.2, the angle of aperture is the opening angle of handle centered on the screw of scissors. Data of Test1 is variance of testing machine. Data of Test2 is variance due to state of clamp in addition to variance of testing machine. Data of Test3 is the result of adding variance between samples. In this test, maximum value is 0.0028 in Test3, which is approximately 5.5% when calculated back to the load. The amount of variance between samples can be used as an indicator of the skill level of craftsmen who made the scissors. Therefore, we measured 5 scissors made by a foreign manufacturer Company X under the same conditions as Test3. The results are shown in Table2.
From the results, we found that the scissors made by Company X had larger variance in the empty cutting load than our products. Although the above is one of examples, we found that quality of scissors can be evaluated by comparing variance.
2.2 Judgment of clearance shape
Compatibility of scissors is determined by clearance shape formed by the two opposing blades. Image of the “clearance” is shown in Fig. 3.
In Fig. 3 (2), the scissors cannot cut object properly because clearance is not made up of one arc. Also, even if it is made of one arc, the scissors cannot cut object properly if clearance is too wide or too narrow.3) This time, we verified whether it is possible to judge quality of this clearance from the empty cutting load. We prepared two samples each of four types of clearance, wide, narrow, middle between wide and narrow, and waved. Fig.4 shows the results of measuring shape of the samples with a three-dimensional measuring machine.
The results are shown in Fig. 5. From the results, we confirmed that the load change felt by the hand could be grasped by the experimental device.
In addition, seven inspectors judged whether the samples used this time could pass the actual inspection. However, the sample with waved clearance was excluded from the sensory test because it could not pass the test for cutting the test material other than the normal clearance inspection. The results are shown in Fig. 6.
We found that in our current inspection, mainly the sample with a narrow clearance (about 0.03 mm) are judged to pass. As described above, we found that there is a correlation between the load change of the empty cutting load and the actual measurement result of the clearance, and the quantitative reference value of the clearance can be determined by combining with the sensory test. From this, we conjectured that judgment of the clearance shape is possible by using the empty cutting load.
We verified possibility of quality evaluation of scissors by measuring the empty cutting load of scissors, and found the following.
Bibliography
1)Kenji Inoue: The proceedings of the 2004 Japanese spring conference for the technology of plasticity, 2004, 195
2)Takashi Iimura: journal of Japan Society for Design Engineering, 48-5 (2013), 233.
3)Kenji Inoue: Journal of Japan Society for Technology of Plasticity,47-540 (2006), 69.
HSC will continue to work on standardizing quality of scissors based on science, so that users can purchase and use scissors without worry.
*Secretary Society: The Japan Society of Technology of Plasticity, Cosponsored by: The Japan Institute of Light Metals, The Japan Society for Precision Engineering , The Japan Institute of Metals and Materials, The Japan Society of Mechanical Engineers, The Society of Materials Science Japan, The Iron and Steel Institute of Japan, The Copper Society of Japan.
Quality Evaluation of Hairdressing Scissors
-Evaluation for Compatibility of Blades-
Kenji Inoue (Tokosha Co., Ltd.) PhD, Member of JSTP
Koshi Yamamura (Yamamura-mfg co., Inc.) PhD, Member of JSME
Toshio Hasegawa (Naruto Scissors Co., Ltd.)
Makoto Hagino (Utsumi Co., Ltd.)
Shinichi Takahashi (Hikari Co., Ltd.)
Takashi Iimura (Iwate Industrial Research Institute) PhD, Member of JSPE
- Introduction
At present, there is no globally unified standard for quality of hairdressing scissors. The main reason for this is that elucidation of the cutting mechanism has not progressed. Specifically,
- Cutting mechanism of scissors is much complicated compared to single blade tool.
- Finishing process of scissors are done by hand, and it is difficult to prepare same quality samples for test.
- Quality is evaluated by user's subjectivity.
- Most of manufacturers of hairdressing scissors are too small to own research division.1)
For changing this situation, we set up Hairdressing Scissors Consortium (HSC) last year. We aim to create environment that hairstylists can choose scissors based on scientific evidence.
We listed evaluation items for quality of scissors (Table1). Left side corresponds to right side of table. Items users evaluate with their feeling is on the left side of table. Parameters that may make the difference is on the right side of table.2) In this report, we report about compatibility of blades.
Table.1 Evaluation items for quality of scissors
2.Testing machine
Fig. 1 is picture of testing machine. This machine consists of air cylinder for clamping scissors, motor for rotating, load cell for measuring force to push up, and rotary encoder for measuring rotation angle. Closing load measured by load cell is transferred to data logger through strain amplifier. Recorded data can be analyzed by PC.
Fig.1 Testing Machine
2.1 Evaluation of magnitude of variance
Because hairdressing scissors are finished by hand, variance of quality is large. Therefore, we measured variance at first. We prepared five samples of same model. At first, we choose one sample and put on the testing machine. We measured necessary force for rotating a blade when screw of scissors is totally tightened, and confirmed approximately 0.34N is necessary.
We adjusted the screw to make maximum closing load without cutting 0.49N±5% of +0.15N.
We measured closing load five times repeatedly (Test1). Next, we measured five times again by using same samples but scissors are put off from testing machine each time to understand variance effected from clamp (Test2). And finally, we adjusted to make maximum closing load without cutting 0.49N, and measures five samples, one time for each (Test3). The data when output voltage of the encoder changes (every 0.52 deg) was extracted, and the average of 5 times was obtained. The variance for each measurement was calculated and compared. The results are shown in Fig. 2.
Fig.2 Variance of each test
In Fig.2, the angle of aperture is the opening angle of handle centered on the screw of scissors. Data of Test1 is variance of testing machine. Data of Test2 is variance due to state of clamp in addition to variance of testing machine. Data of Test3 is the result of adding variance between samples. In this test, maximum value is 0.0028 in Test3, which is approximately 5.5% when calculated back to the load. The amount of variance between samples can be used as an indicator of the skill level of craftsmen who made the scissors. Therefore, we measured 5 scissors made by a foreign manufacturer Company X under the same conditions as Test3. The results are shown in Table2.
Table2 Comparison of variance values with overseas products
From the results, we found that the scissors made by Company X had larger variance in the empty cutting load than our products. Although the above is one of examples, we found that quality of scissors can be evaluated by comparing variance.
2.2 Judgment of clearance shape
Compatibility of scissors is determined by clearance shape formed by the two opposing blades. Image of the “clearance” is shown in Fig. 3.
(1)Good example
(2)Bad example (Clearance does not draw one arc)
Fig.3 Images of clearance
In Fig. 3 (2), the scissors cannot cut object properly because clearance is not made up of one arc. Also, even if it is made of one arc, the scissors cannot cut object properly if clearance is too wide or too narrow.3) This time, we verified whether it is possible to judge quality of this clearance from the empty cutting load. We prepared two samples each of four types of clearance, wide, narrow, middle between wide and narrow, and waved. Fig.4 shows the results of measuring shape of the samples with a three-dimensional measuring machine.
Fig. 4 Slope of load change (Empty cut load 0.4N)
The results are shown in Fig. 5. From the results, we confirmed that the load change felt by the hand could be grasped by the experimental device.
Fig.5 Clearance measurement results
In addition, seven inspectors judged whether the samples used this time could pass the actual inspection. However, the sample with waved clearance was excluded from the sensory test because it could not pass the test for cutting the test material other than the normal clearance inspection. The results are shown in Fig. 6.
Fig.6 Sensory test results of sample scissors
We found that in our current inspection, mainly the sample with a narrow clearance (about 0.03 mm) are judged to pass. As described above, we found that there is a correlation between the load change of the empty cutting load and the actual measurement result of the clearance, and the quantitative reference value of the clearance can be determined by combining with the sensory test. From this, we conjectured that judgment of the clearance shape is possible by using the empty cutting load.
- Conclusion
We verified possibility of quality evaluation of scissors by measuring the empty cutting load of scissors, and found the following.
- The variance can be evaluated by measuring the empty cutting load of multiple samples and comparing the variance at each angle.
- The clearance shape of the scissors can be estimated by comparing the slope of the load change of the empty cutting load.
Bibliography
1)Kenji Inoue: The proceedings of the 2004 Japanese spring conference for the technology of plasticity, 2004, 195
2)Takashi Iimura: journal of Japan Society for Design Engineering, 48-5 (2013), 233.
3)Kenji Inoue: Journal of Japan Society for Technology of Plasticity,47-540 (2006), 69.